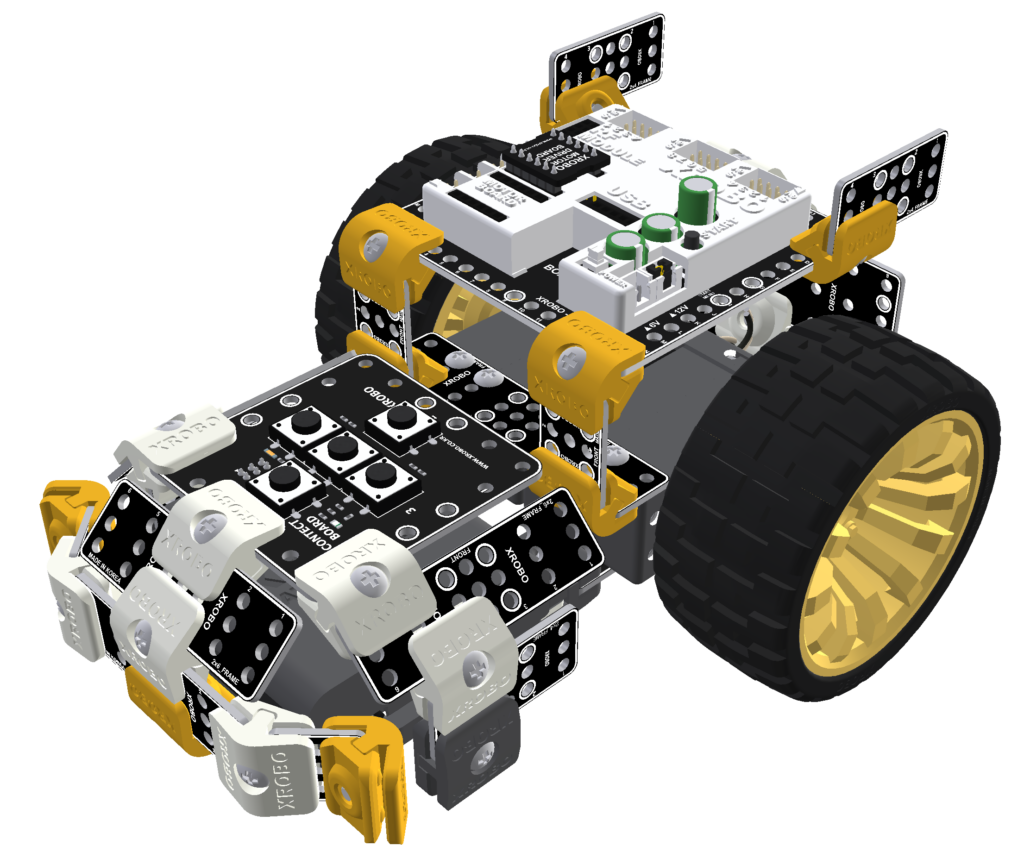
1. Robot Assembly
- Please refer to the manual for assembling the robot.
- Ensure all components are properly connected.
2) Verifying Cable Connections
-
Left DC Motor with the left wheel
→ Connect to the M1 port on the CPU board. -
Right DC Motor with the right wheel
→ Connect to the M2 port on the CPU board. -
X-Keypad used for controlling the robot
→ Connect to the IN1 port on the CPU board.
2. Code Upload & Robot Operation
1) If You Are Not Coding
- ① Turn on the power to the CPU board.
- ② Press and hold the START button for more than 2 seconds. Release it when you hear the "Do Re Mi Fa Sol La Ti Do" melody.
- ③ Press the START button 10 times to select the "High Mi" tone.
2) If You Are Coding the Program Yourself
① Preparing for Upload
- Ensure mBlock is installed on your computer. If not, please install mBlock.
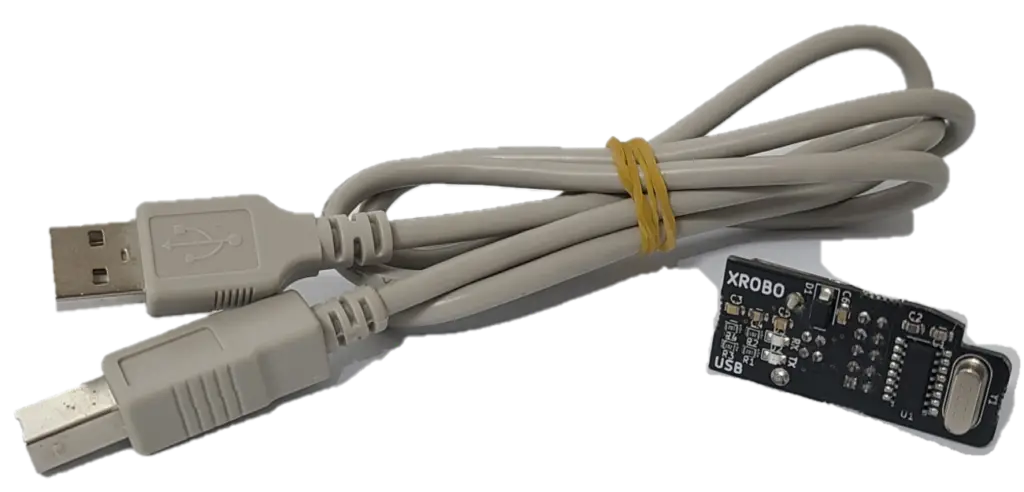
- To operate the robot, you will need a download board and a download cable. If you do not have these components, please purchase them.
② Coding the Program
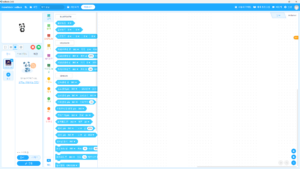
- Launch mBlock and freely code your program by referring to the coding examples or the manual.
③ Uploading the Code
- Upload the code to the robot by following the instructions on the upload method page or video (starting at 34 seconds).
④ Operating the Robot
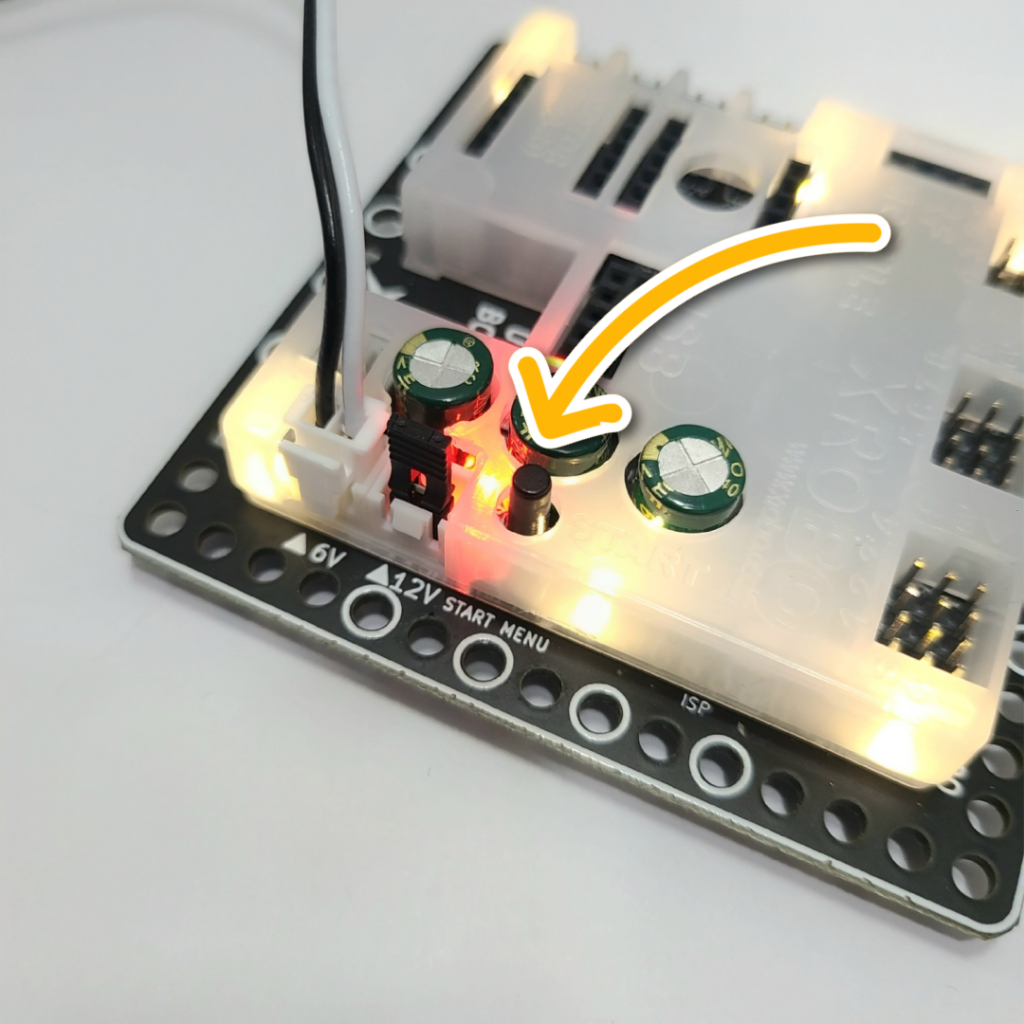
- ① Turn on the power to the CPU board.
- ② Briefly press the START button on the CPU board and then release it.
- ③ Turn on the power to the remote control and have fun controlling the robot.
3. Coding Examples
1) Moving the Robot Forwards and Backwards
Move Forward
Let’s make the robot move forward at a speed of 20 for 1 second.
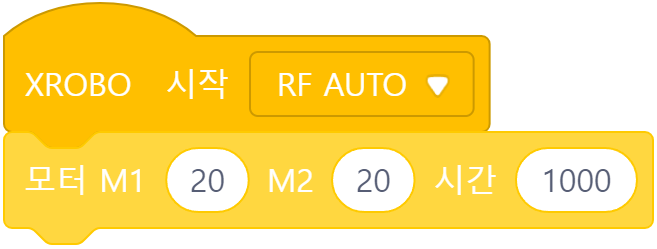
Since the DC motors with wheels are connected to the M1 and M2 ports, set the speed of ‘M1’ and ‘M2′ to ’20’.
Move Backward
Let’s make the robot move backward at a speed of 20 for 1 second.
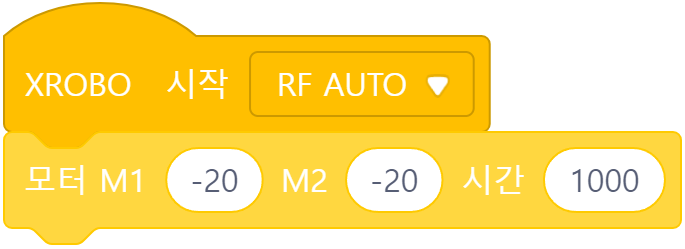
If the speed value is prefixed with a ‘-‘, the DC motor will rotate in the opposite direction.
2) Turning the Robot Left and Right
Left Turn
Let’s make the Robot turn left by stopping the left wheel and moving the right wheel forward.
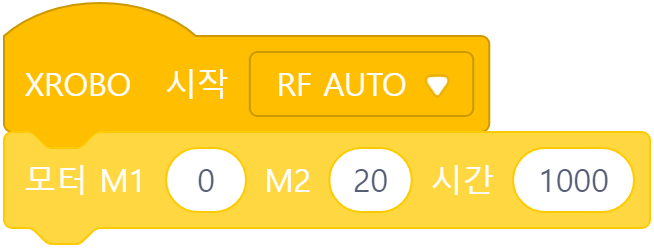
Since the right DC motor with the wheel is connected to the M2 port, set the speed of ‘M2′ to ’20’.
Right Turn
Let’s make the Robot turn right by stopping the right wheel and moving the left wheel forward.
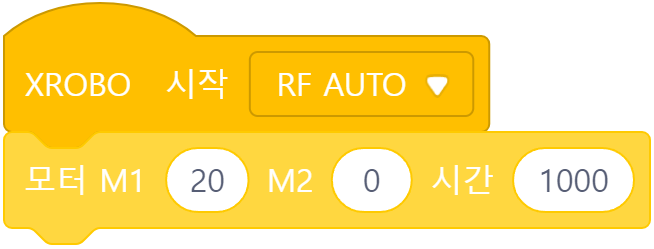
Since the left DC motor with the wheel is connected to the M1 port, set the speed of ‘M1′ to ’20’.
3) Controlling the Robot with the X-Keypad
Press a button on X-Keypad
Let’s program the robot to perform specific actions when a button is pressed on the X-keypad:
- Button 1: Move Forward
- Button 2: Move Backward
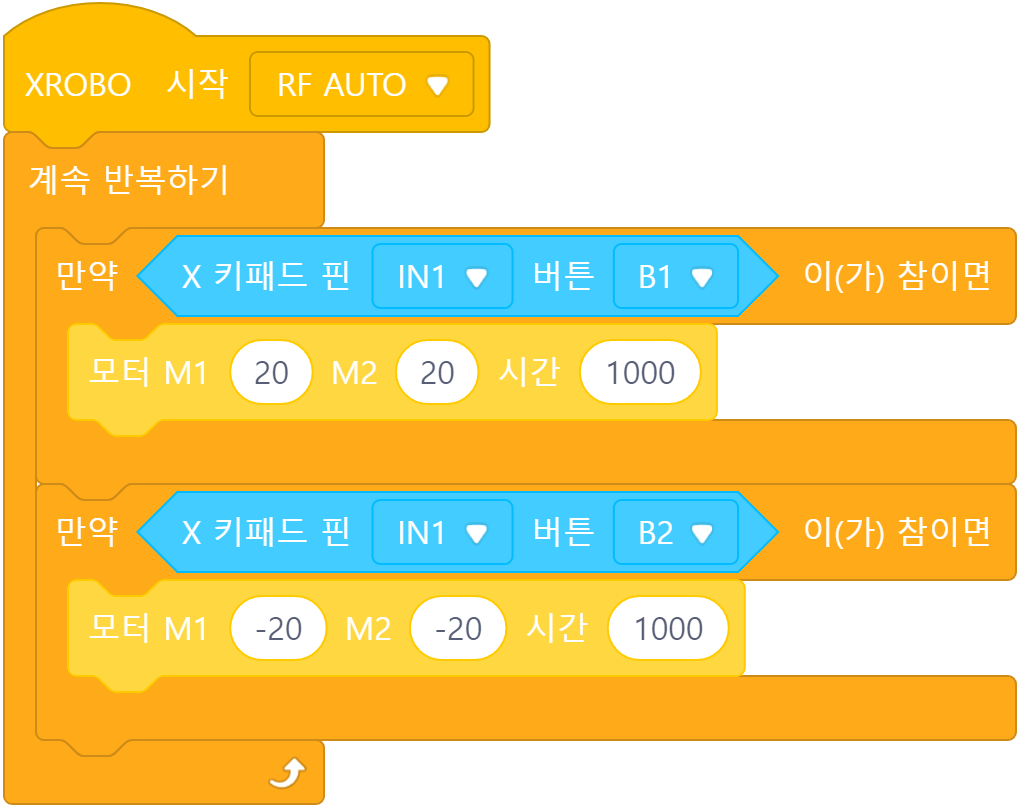
X-키패드가 IN1 포트에 연결되어 있으므로 ‘IN1’을 선택합니다.
Press a button on X-Keypad
Let’s program the robot to perform specific actions when a button is pressed on the X-keypad:
- Button 1: Move Forward
- Button 2: Move Backward
- Button 3: Rotate Left in Place
- Button 4: Rotate Right in Place
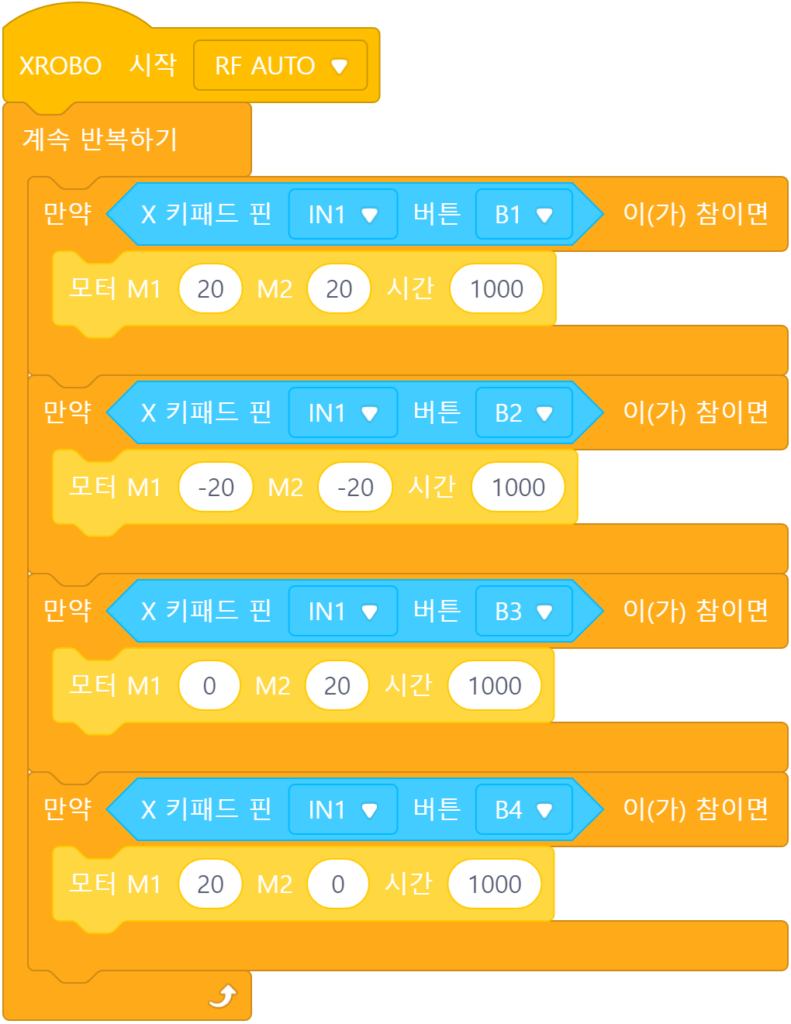
4. Troubleshooting Robot Issues
1) When the Power Does Not Turn On
- Ensure the batteries are inserted with the correct polarity, matching the ‘+’ and ‘-‘ signs.
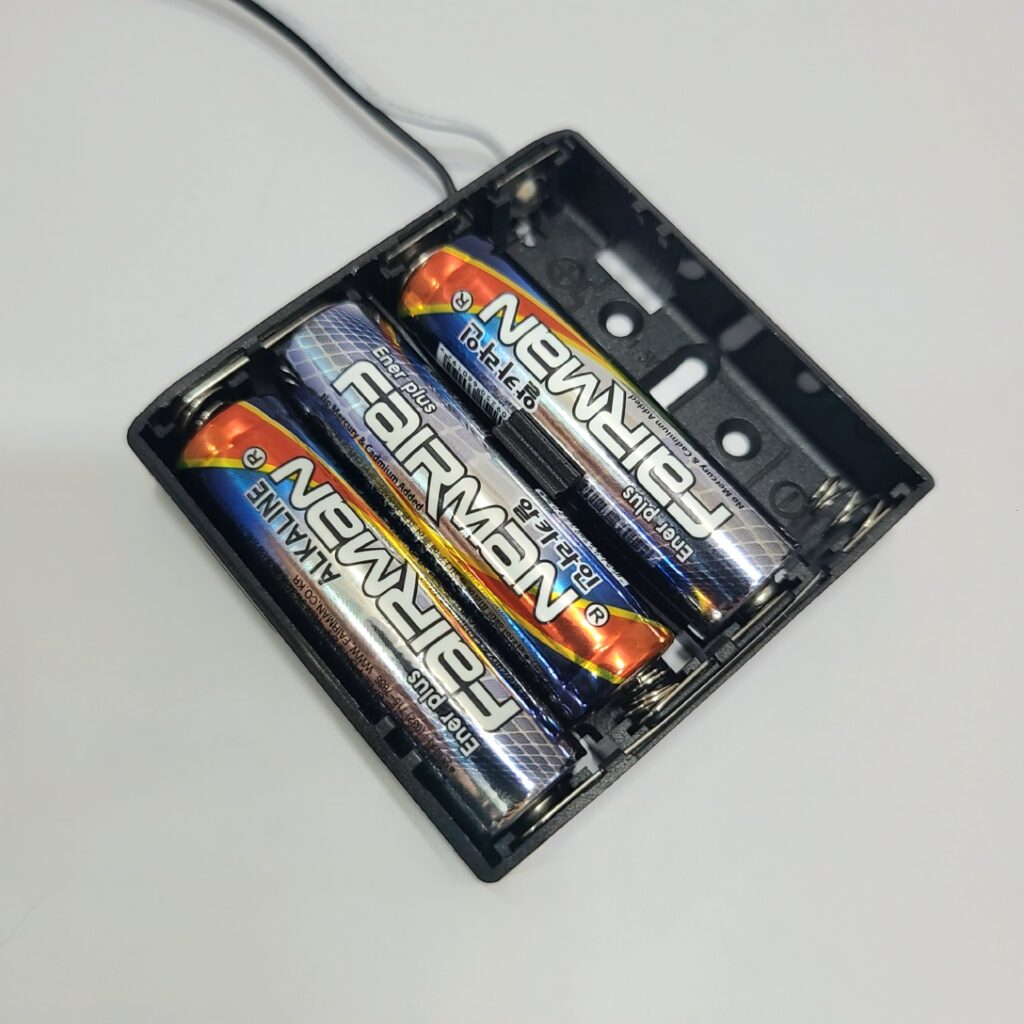
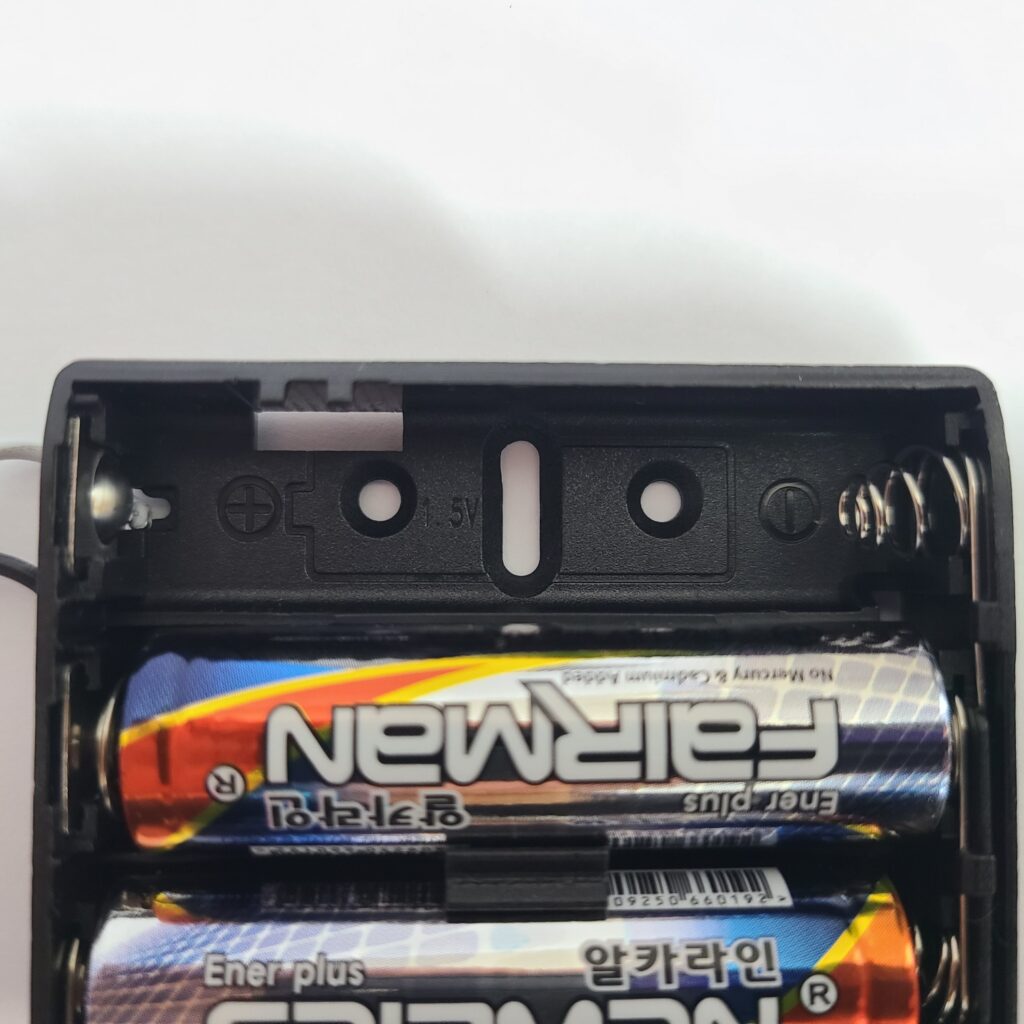
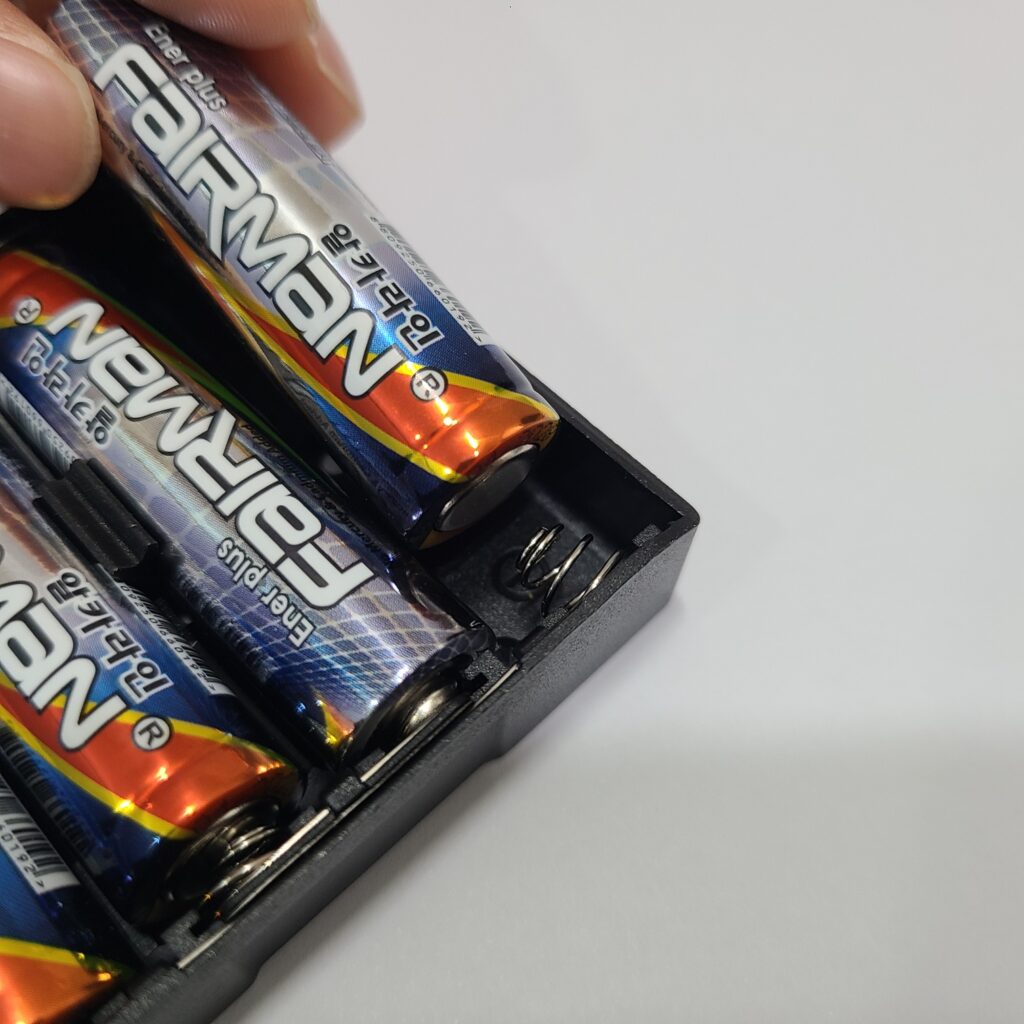
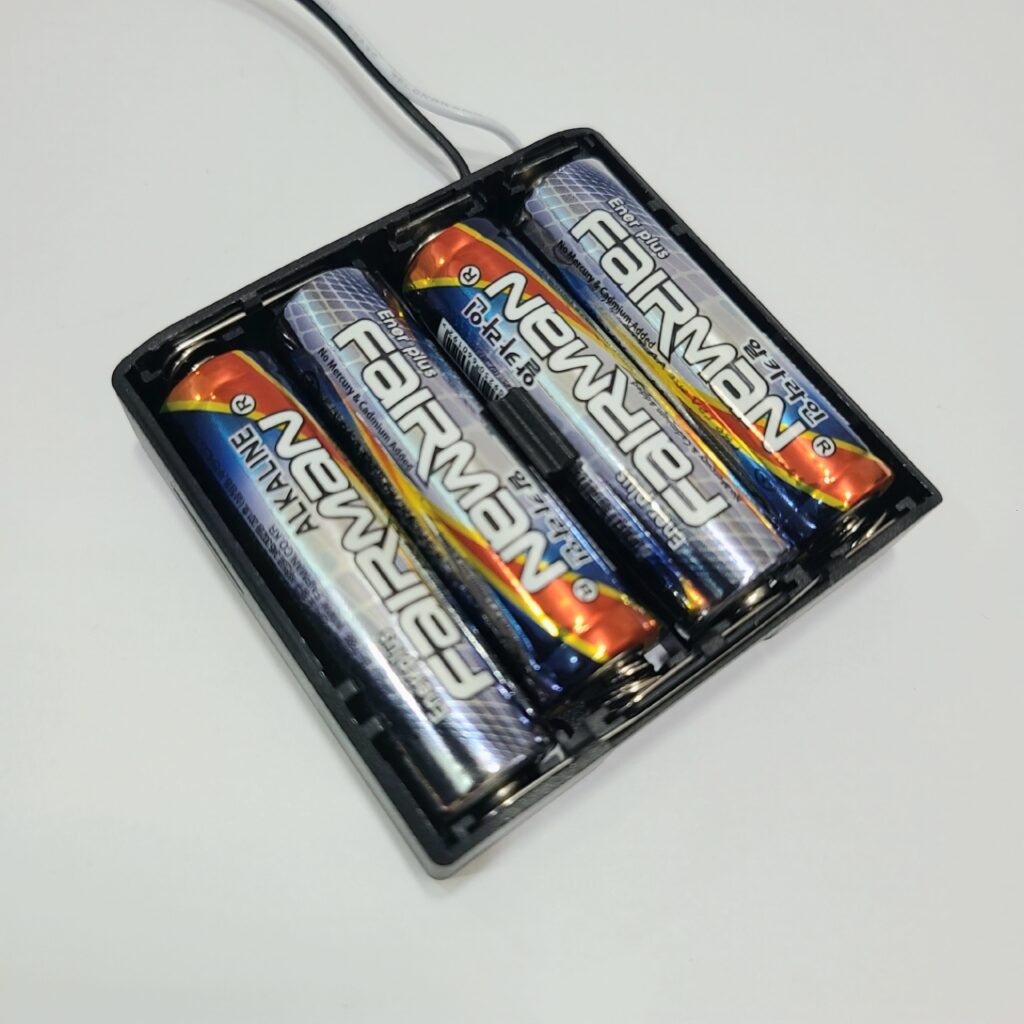
- Verify that the jumper cap is properly inserted into the 12V power connector on the CPU board.
- If there is no jumper cap available, use a 3×8 bolt to connect to the 12V power connector as an alternative.
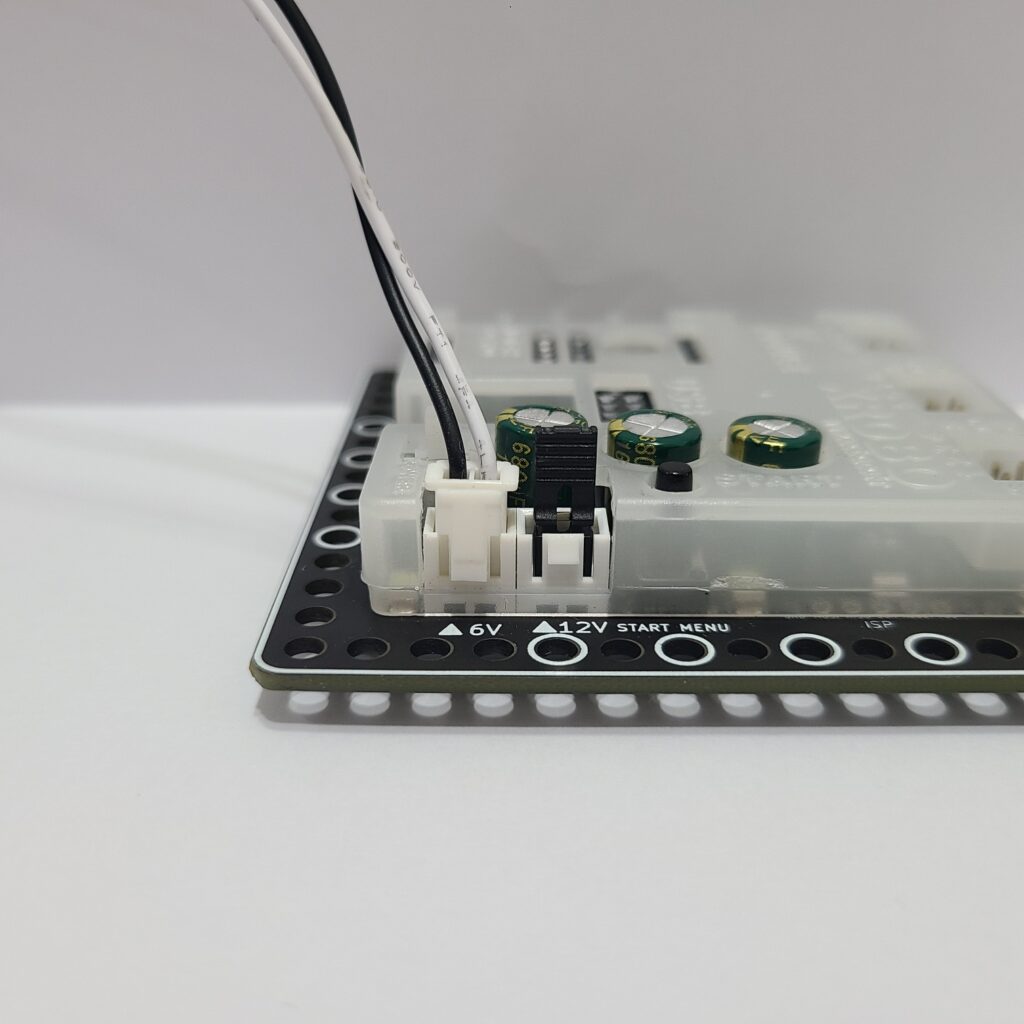
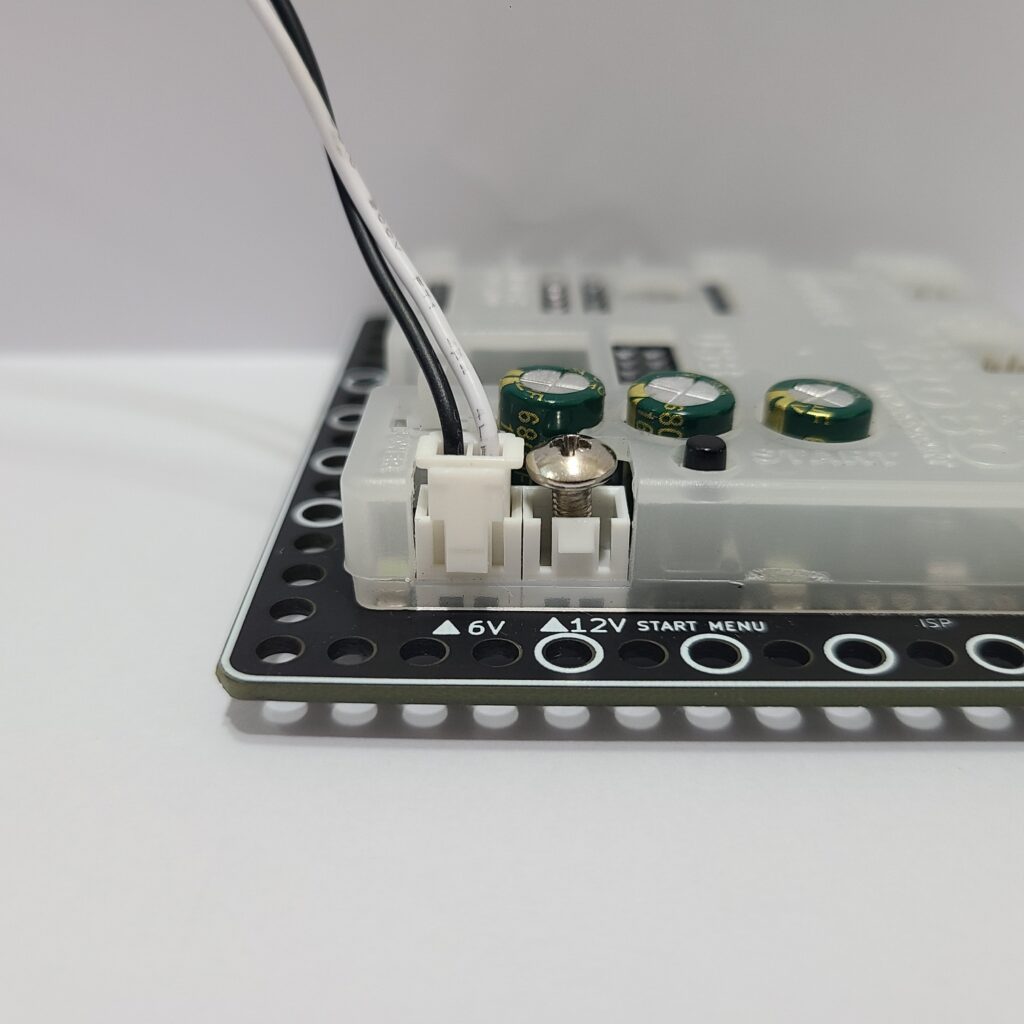
- Inspect the battery pack cable for any breaks or disconnections.
- Ensure that the battery pack cable is securely connected to the 6V power connector on the CPU board.
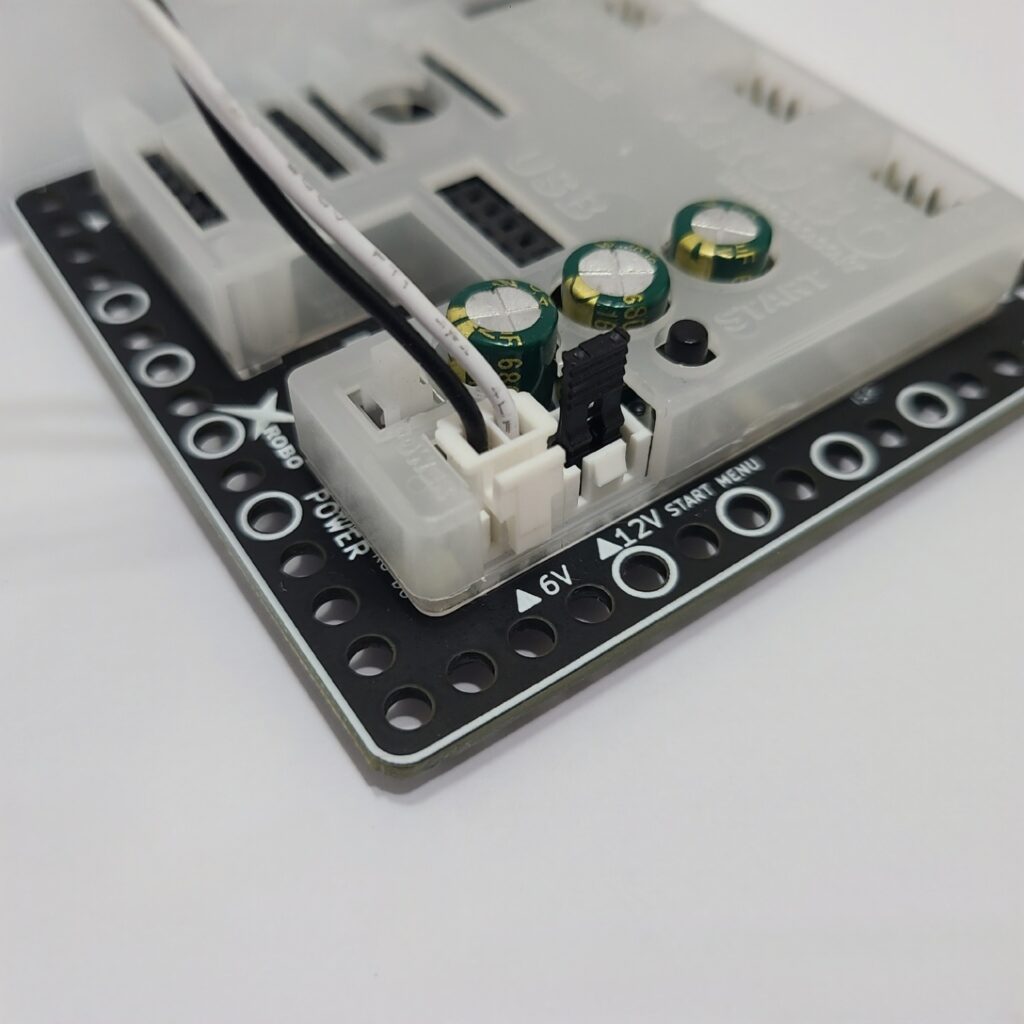
2) When the DC Motor Does Not Rotate / Rotates in the Wrong Direction
- Ensure that the motor cables are correctly connected to the motor port.
- Check the motor cables for any signs of disconnection or damage.
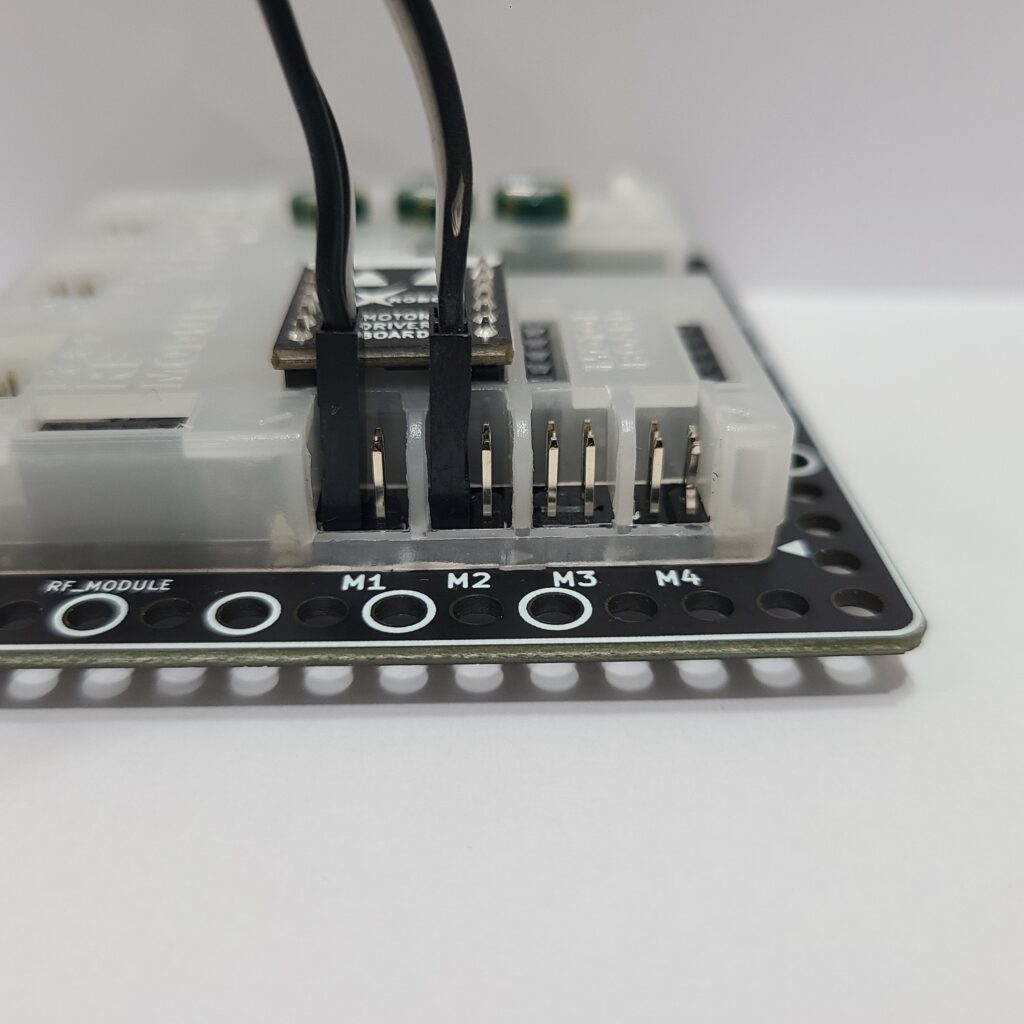
- Confirm that the motor cables are inserted vertically into the motor ports on the CPU board. If connected horizontally, the motor may not rotate.
- Ensure the black wire of the motor cable is aligned with the arrow on the CPU board case. If connected in reverse, the DC motor will rotate in the opposite direction.
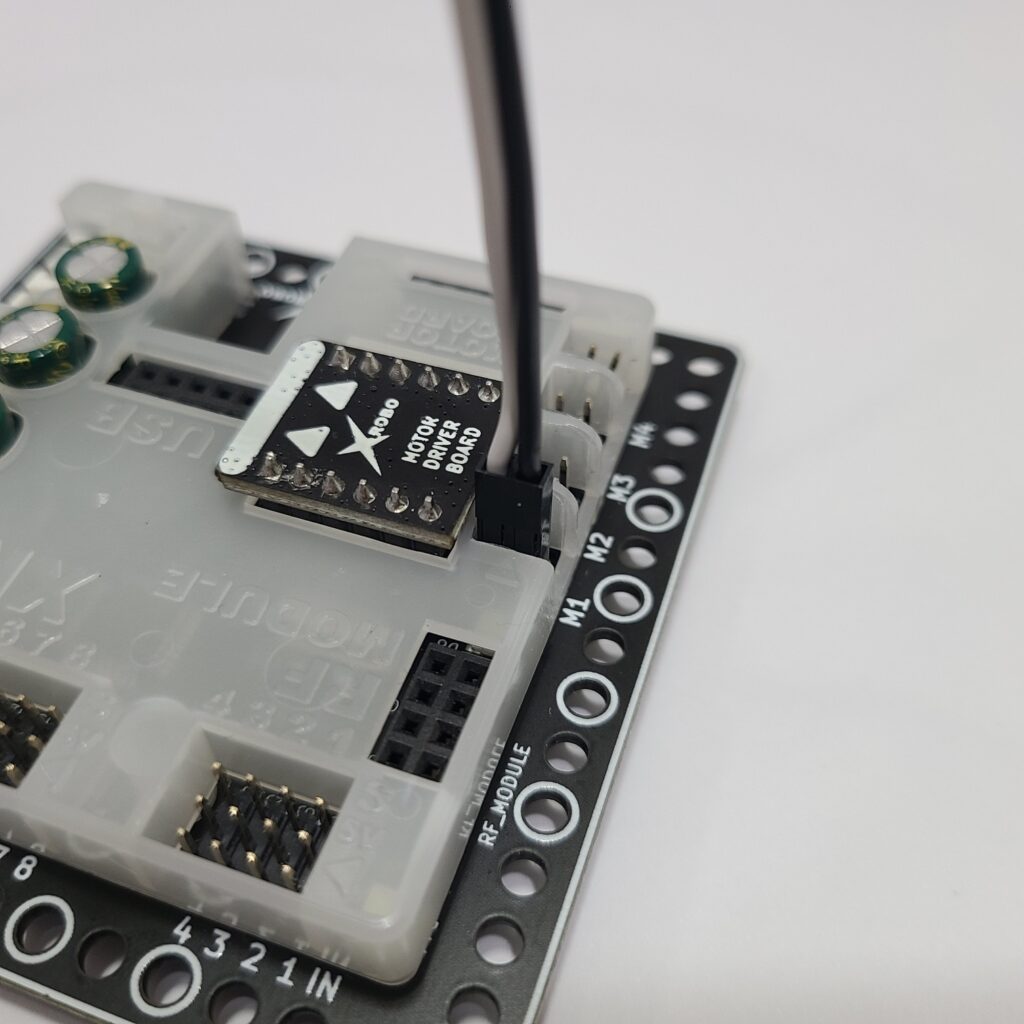
- If the DC motor driver board is not inserted according to the assembly diagram, do not turn on the power. Insert it correctly as per the assembly diagram to avoid overheating risks during operation.
- If the DC motor driver board is not inserted, place it properly and then turn on the power to check the operation.
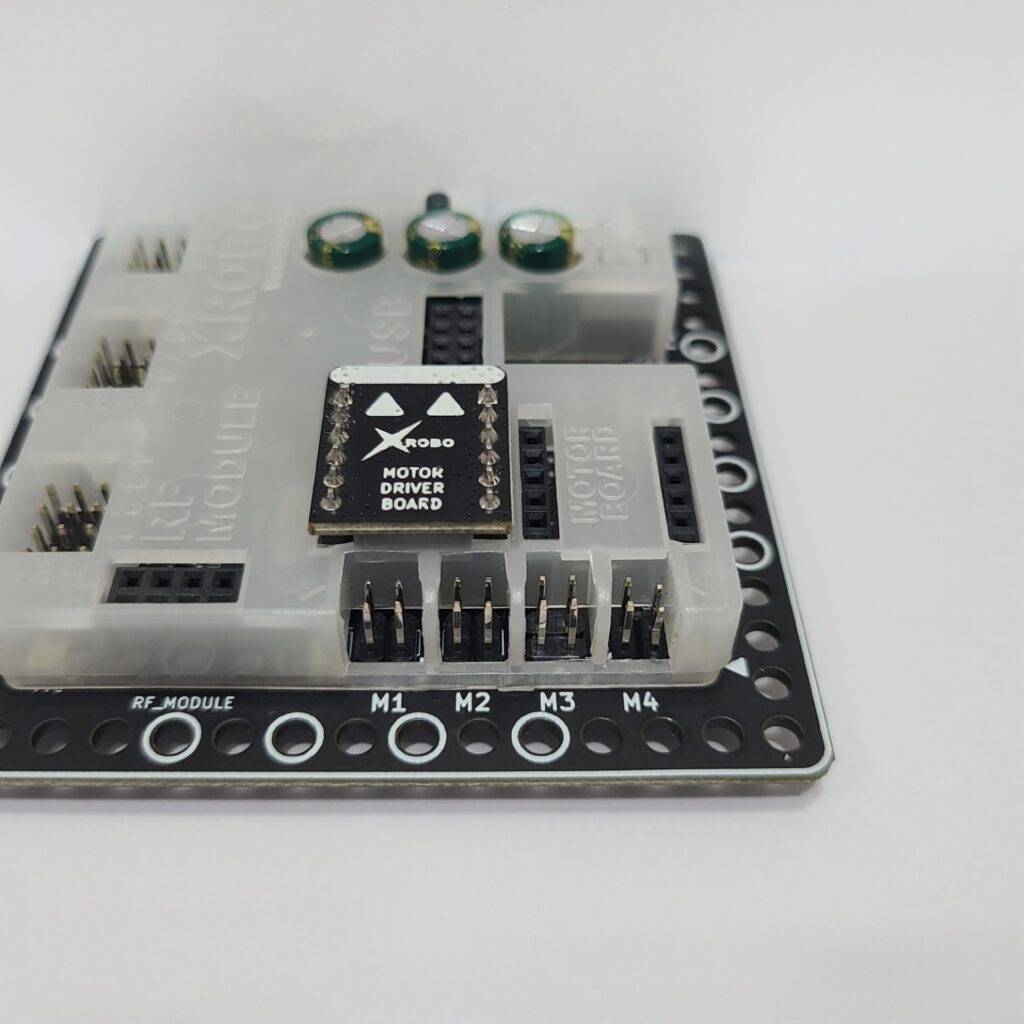
3) When the Robot Operates Abnormally
- Ensure that the shafts of the left and right DC motors are assembled so that they face the back of the robot. If the motor shafts are incorrectly assembled, the wheels may catch on the frame, preventing proper operation.
- Verify that the black wire of the 3-PIN cable is connected to the side with the white line on the X-keypad pin. (Inserting the 3-PIN cable in reverse can cause a short circuit, resetting the CPU board.)
- Ensure that the black wire of the 3-PIN cable is aligned with the arrow on the CPU board case. (Reversing the 3-PIN cable can cause a short circuit, resetting the CPU board.)
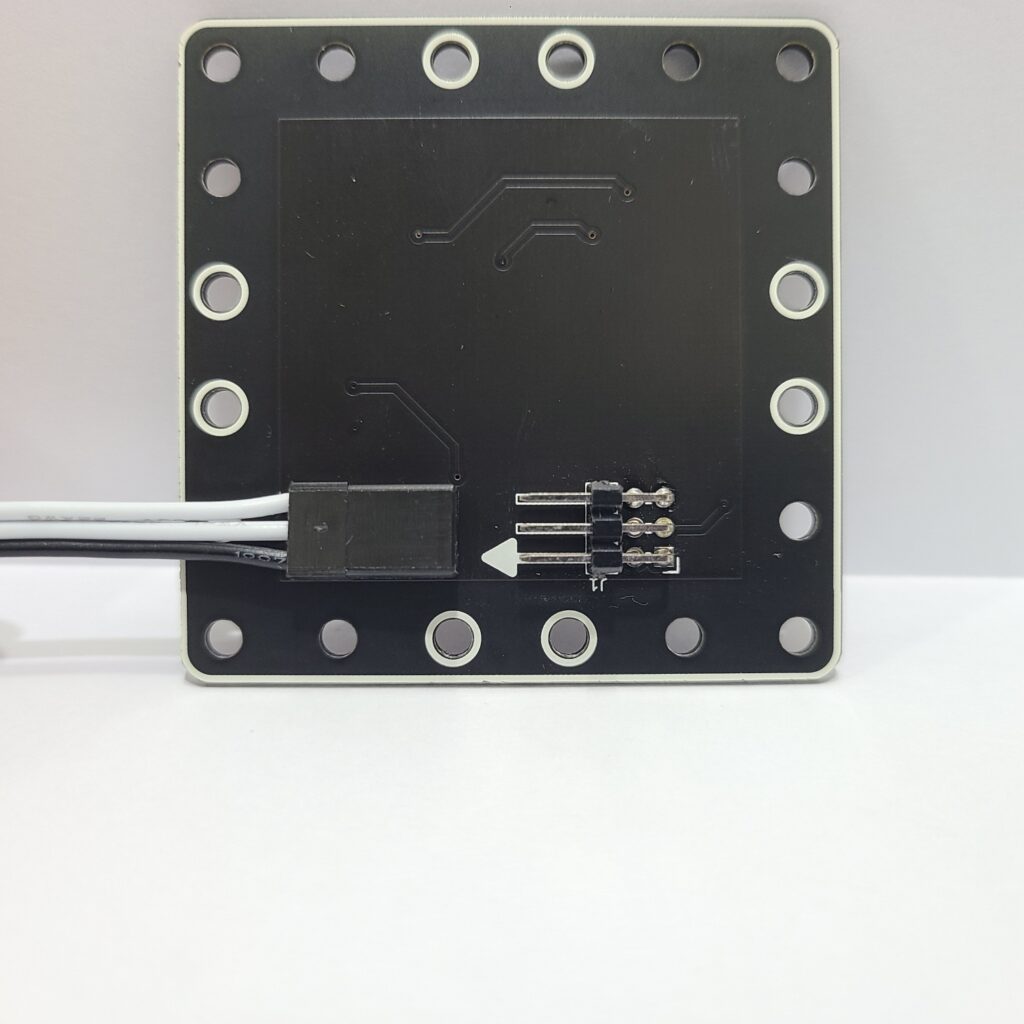
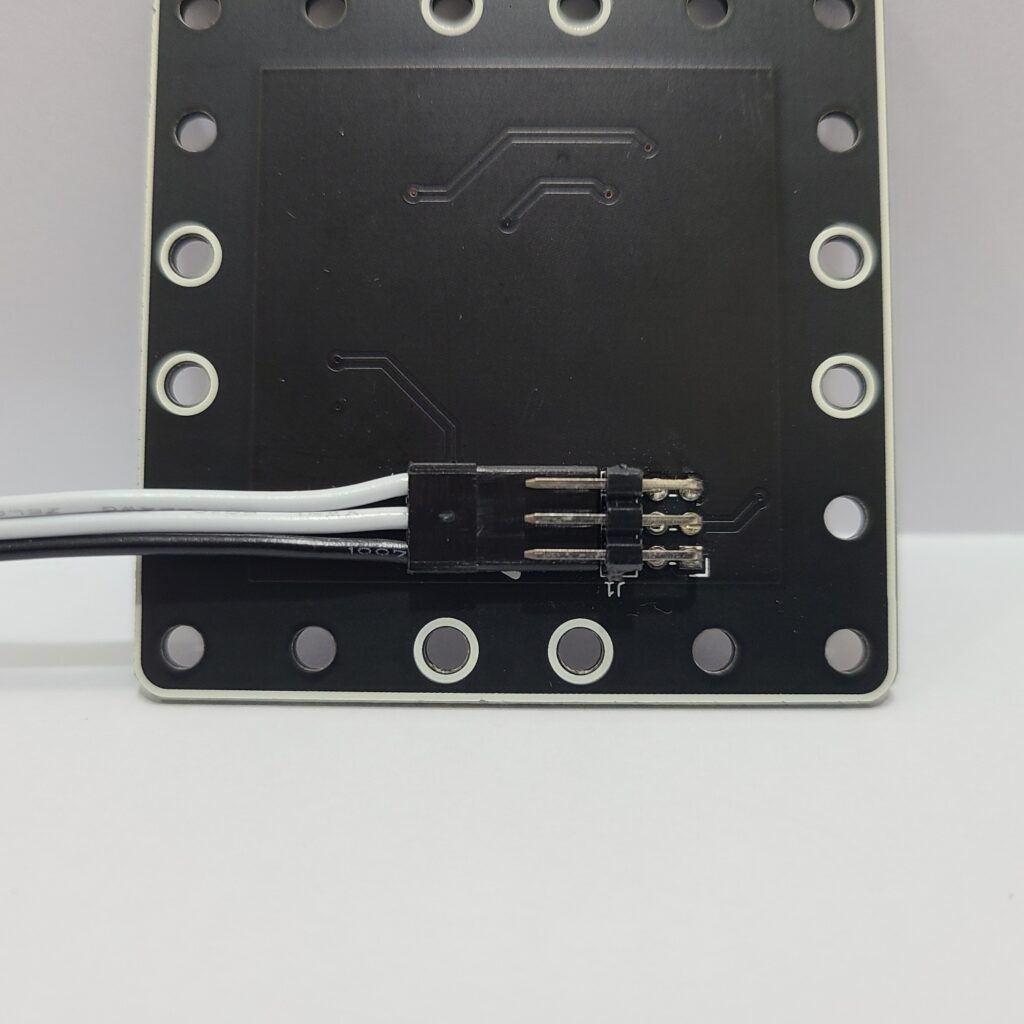
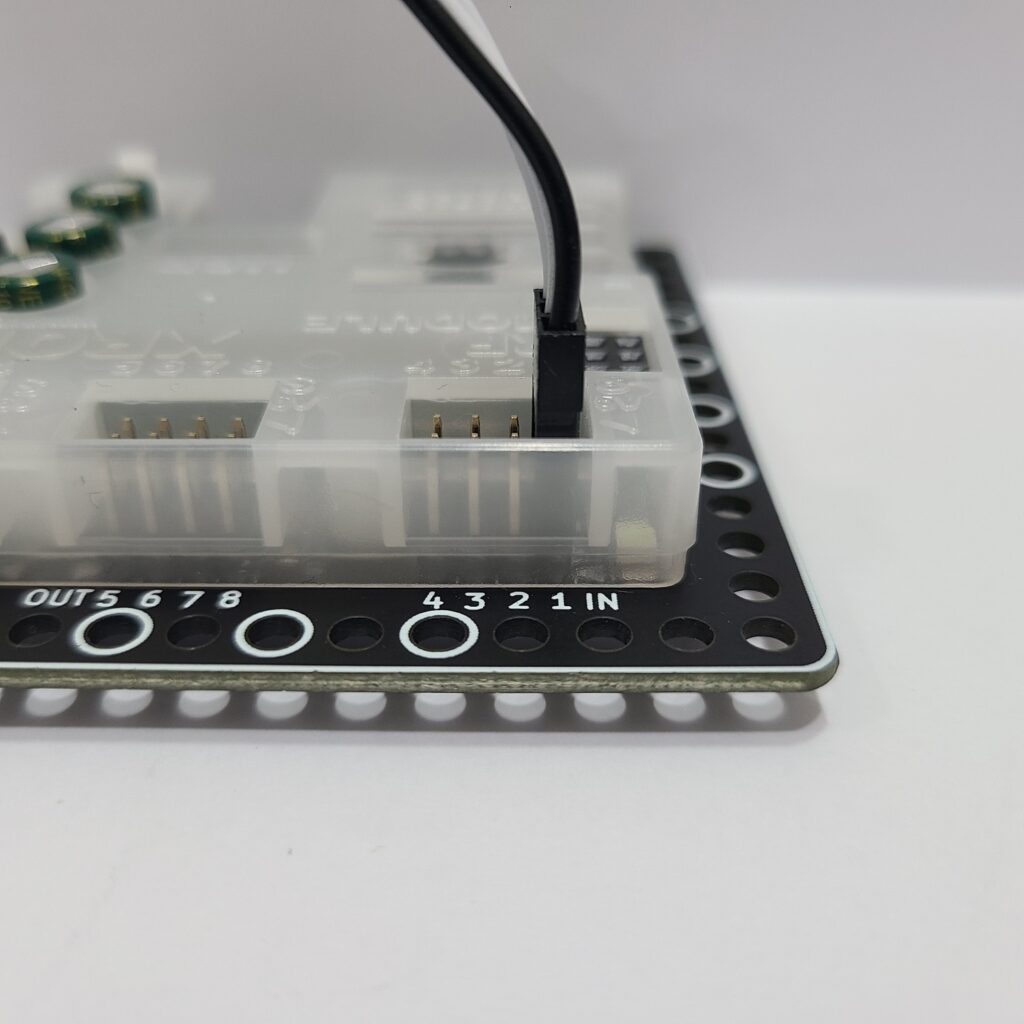
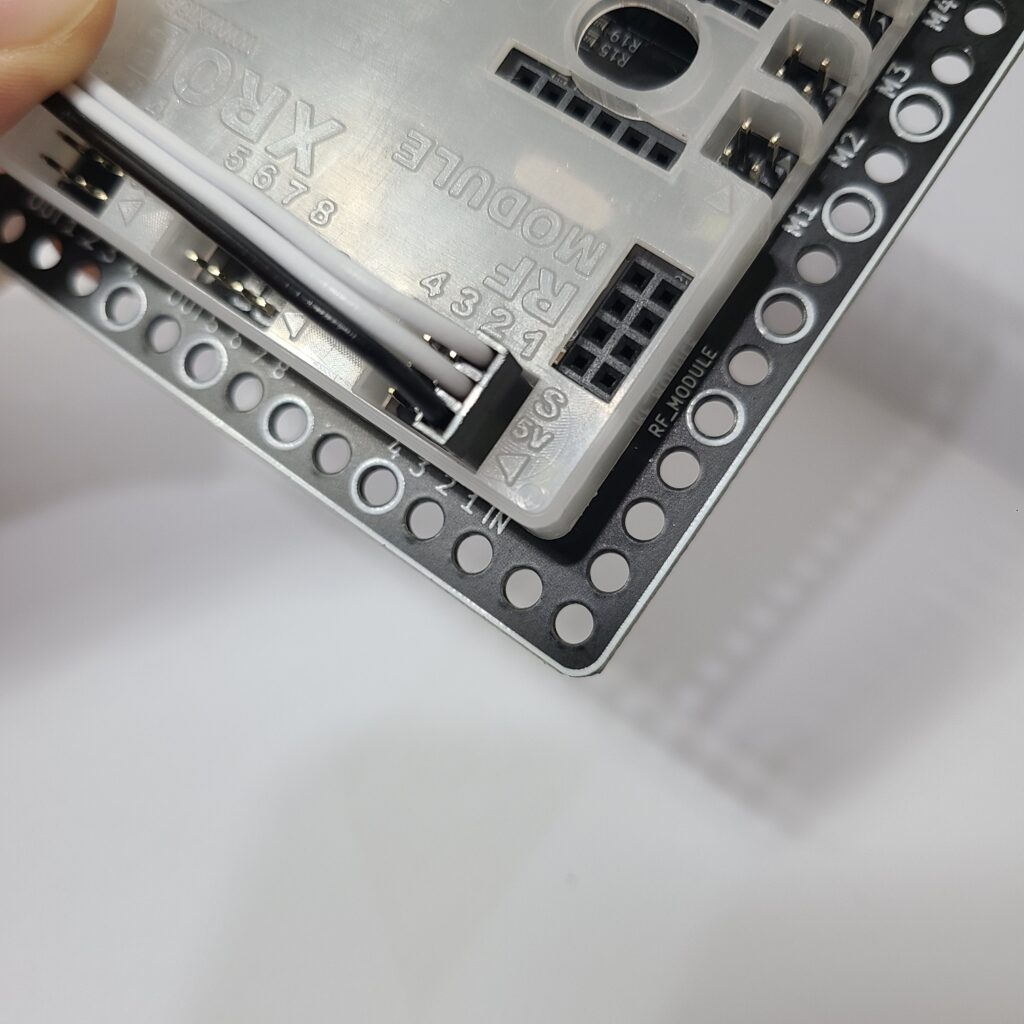
- Check that the cables are not caught in the drivetrain. If the cables are entangled with the drivetrain, the robot may not function properly.
- If you want to repeat the last coded action, press the START button on the CPU board instead of the X-Keypad button to execute the code.
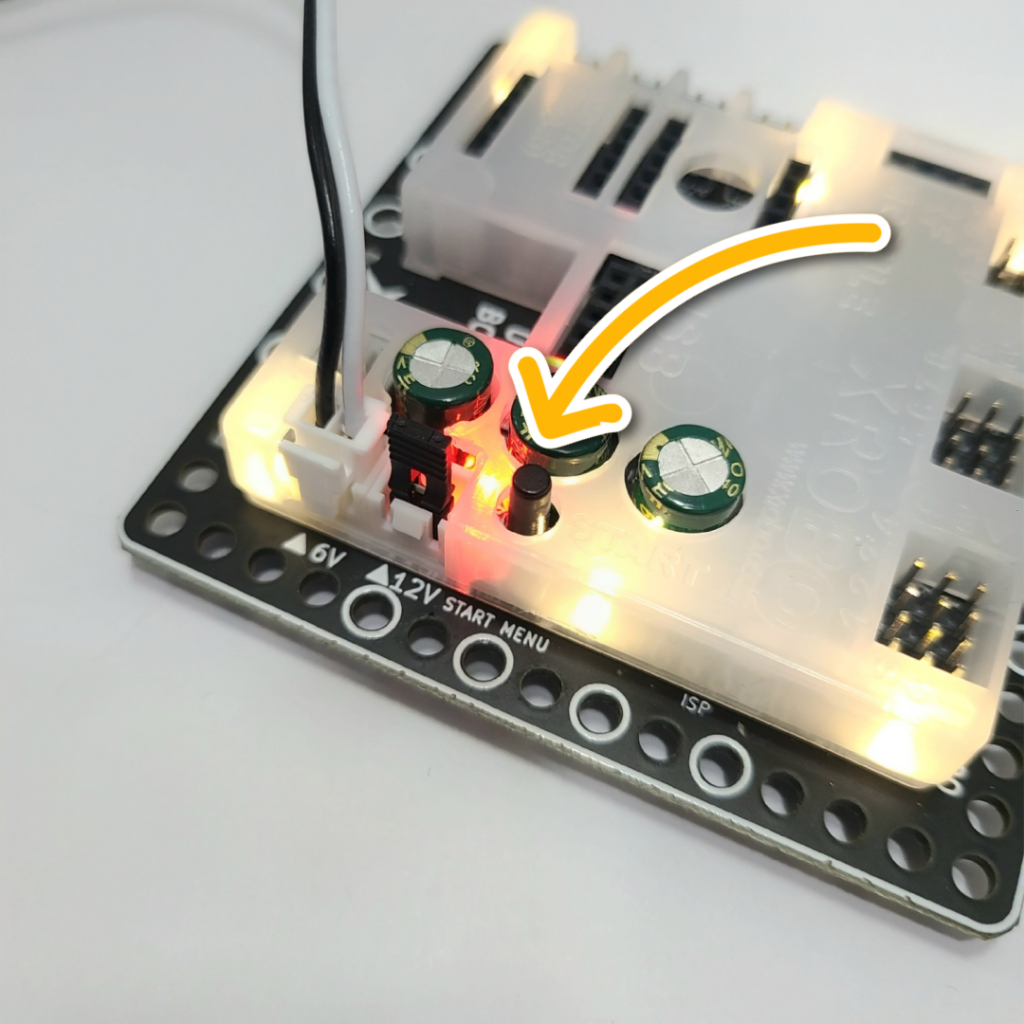